There are a
couple of real advantages to the quick build kit. Namely
the installation of the firewall, the main bulkheads along with the
main
and rear spars. The disadvantages are that you then must work
around
these preinstalled componets to install hard points for controls and
seatbelts.
You are also required to cut out the front and rear seat backs
from
the preinstalled parts. The advantage to not getting the quick
build
are being able to install many of the hardpoints on the work bench
before
installing in the lower fuselage. I am not sure how much time
difference
there is but it sure is a lot easier on the back. |
|
|
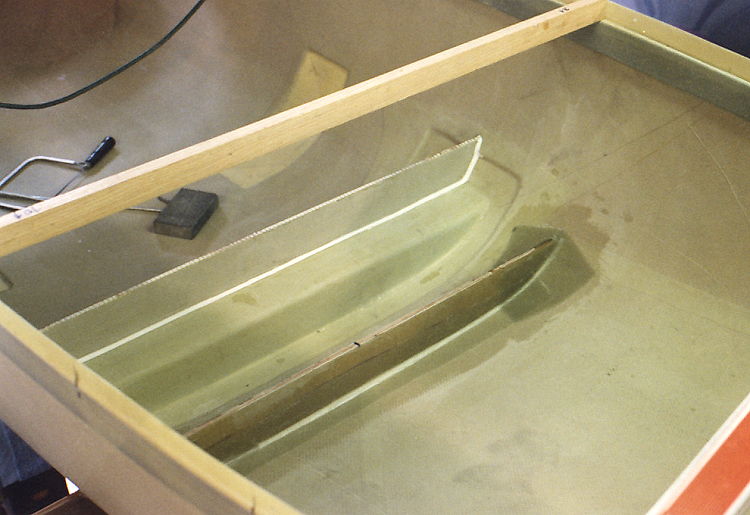 |
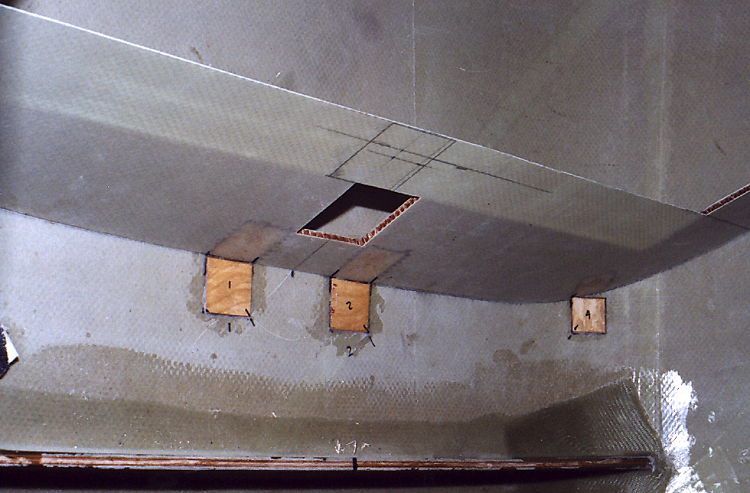 |
Initial start of bonding
of the rear spar. The 1 x 2 is an oak spacer used to keep the
fuselage at the correct width until interior bulkheads are installed. |
This shows the lower portion of the rear seat back
being fit for installation. I installed all hard points for the
rear seat belts before installing the seat back. Saves a lot of
time. |
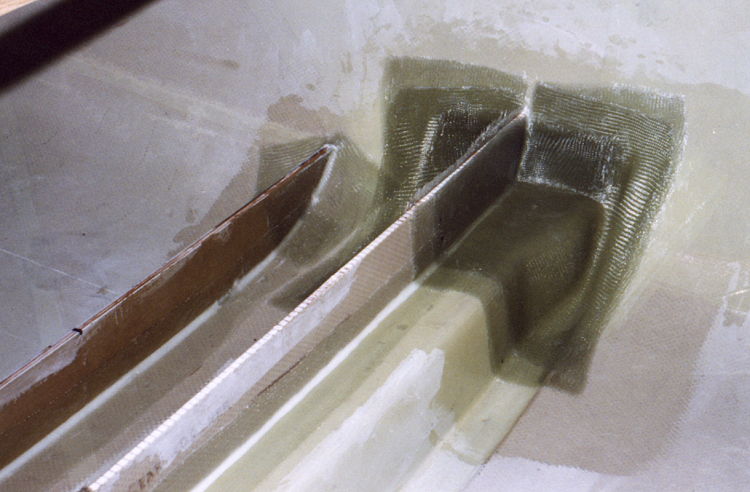 |
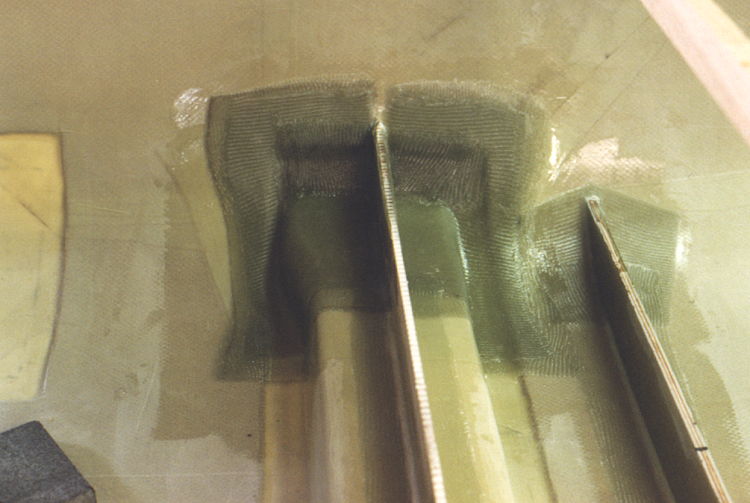 |
Here is one view of the
layups for the rear spar and the stiffner for the landing gear recess. |
A view from the other side showing the rear spar and gear re-enforcement.
|
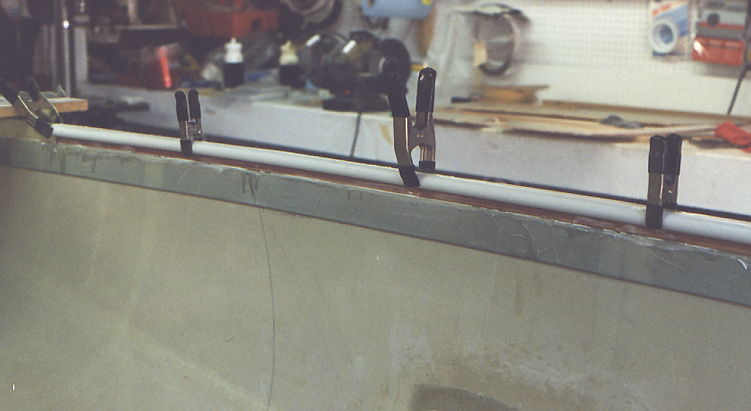
|
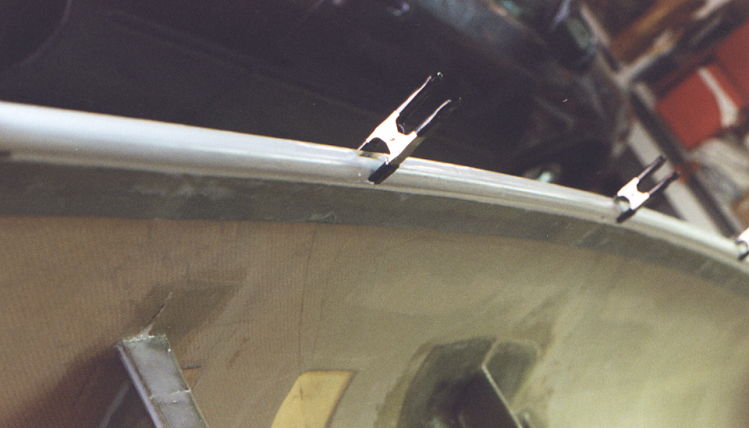
|
A shaped length of 1/4 inch
plywood has been bonded above the longeron. The PVC conduit is
being bonded on above that. |
A micro filler has been used
to fill the gap between the sides and the PVC conduit. Micro Filler is
also used to fill and level below the PVC. |
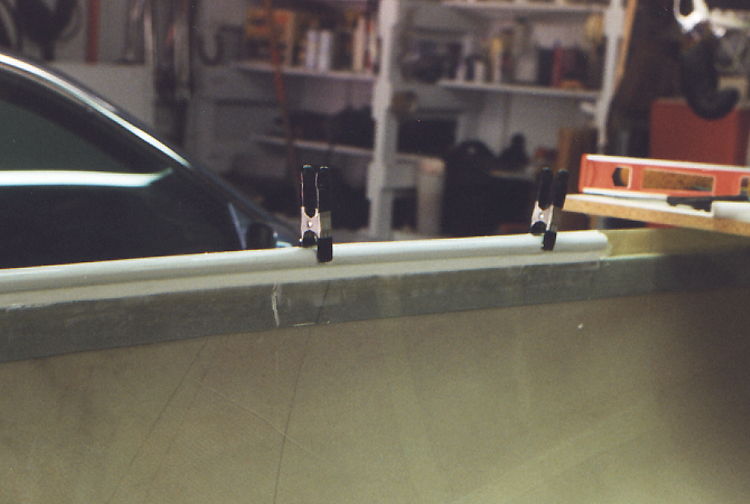
|

|
This shows the conduit in
place and ready to add the two plys of glass to complete the conduit
and add strength to the fuselage sides. |
A total waste of film and
paper but required from time to time just to prove that I am me and I
am the builder. |